The tool problem need to consider in the machining process
Each processing plant to make a decision: Is a homemade tool or outsourcing tool. Another similar decision: should re-grinding tool or spend money for professional regrinding services. There is also a need to consider the tool coating: It should be what kind of coating; circumstances under which a coated tool; tool regrinding the need to re-coating.
There are a small part of the manufacturer of solid carbide rough grinding and production of their own with most of the cutting tool. In addition to producing their own standard tool manufacturers also have special tools designed for specific processing. Some self-grinding tool processing workshops declared their homemade tool to get higher than the purchased tool machining accuracy.
Machining, the tool life is based on a defined processing time to achieve the required processing time, all knives have to be re-grinding. Those who own grinding workshop of the new tool can also regrinding used knives, new knives, tool grinder both grinding and heavy grinding of tool wear. However, some workshop reflect the regrinding of the tool life will be reduced. To ensure that we produce high quality parts, finishing usually need to use a new tool regrinding of the tool is in turn used for roughing.
Not recommend the use of coated tools when milling titanium alloy surface speed of less than 70sfm (21m/min). The low speed rough milling of cobalt high speed steel tools. If some kind of coating is very important for the new tool, tool regrinding and recoating the same coating is equally important. Re-coating will be a logistics problem, because most of the processing plant are not tool coating equipment, the usual practice is the tool to a professional coating services company to recoat.
When the smaller diameter of the tool needs to be longer hanging stretch the amount of the workpiece deep, often because of the tool deflection is too large and can not achieve effective cutting. The usual solution is to taper shank tool rigidity and better, but this tool cost is relatively high. A lower cost solution is to use hot charging tool chuck rigidity required to maintain a large overhang of the tool. This method can be maintained at a lower cost, because using the standard hot charging chuck, and only need to replace the worn tip can. Milling titanium alloy, hot charging chuck is an ideal choice.
Many tool installed on the machine before, and the tool chuck dynamic balance. In order to ensure the right balance, you can use the tool chuck drill weight loss, or increase the screw weight gain method. If all tools are using the same mode of operation, the tool balanced management is also relatively easy. Chuck / tool combination on a dynamic balancing machine dynamic equilibrium, static equilibrium is difficult to meet the requirements of high-speed processing.
Any processing speed of more than 8,000 r / min the tool must be balanced. However, regardless of the speed high and low, it is best to balance all chuck / tool combination, which will help to prolong spindle life. One without the balance of the tool in the high-speed machining may soon damage the spindle of a value of $ 50,000 to replace the spindle, machine tools may have to shut down two weeks time.
Latest News
Contact Us
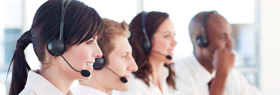
Name: Nina
Tel: 0086-0769-81177281
Fax: 0086-0769-81177281
Mobile: 0086-13712515491
E-mail: [email protected]
Skype: toolsharpener
QQ: 19641516791
WeChat: 0086 13712515491
Whatsapp: 0086 17727718926
Add: No 1 industrial avenue, Hengli Town,Dongguan city,Guangdong provience,China